Operation of PMMC Instrument
Most analogue (pointer-on-scale) instruments rely on three factors for their operation: a deflecting torque; a restoring torque; and a damping torque.
Deflecting Torque: Essentially, a moving coil meter is a current measuring device. The current to be measured is passed through a multi-turn coil suspended between the poles of a permanent magnet. The coil is made from fine copper wire which is wound on to a light aluminium former. Thus the motor effect, is utilised.
Since the wire is of small diameter, and the aluminium former is also very light, then this assembly has very little inertia. This is an essential requirement, to ensure that the instrument is sufficiently sensitive. This means that it can respond to very small deflecting torques. In order to improve the sensitivity further, the friction of the coil pivots must be minimised. This is achieved by the use of jewelled bearings as shown in Fig. 1 .
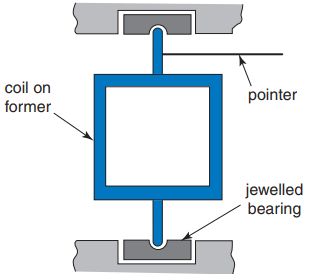
When a current is passed through the coil it will rotate under the influence of the deflecting torque. However, if the ‘starting ’ position of the coil is as shown in Fig. 2, then it will finally settle in the vertical position, regardless of the actual value of the current. The reason is that the effective perpendicular distance from the pivot point (the term r sin θ in the expression F = 2NBIIr sinθ ) decreases to zero at this position.
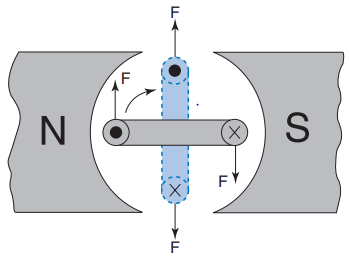
Another way to explain this is to consider the forces acting on each side of the coil. These will always act at right angles to the main flux. Thus, when the coil reaches the vertical position, these forces are no longer producing a turning effect. This means that the instrument is capable of indicating only the presence of a current, but not the actual value.
Hence, the deflecting torque (which is dependent upon the value of the coil current) needs to be counter-balanced by another torque.
Restoring Torque: This is the counter-balancing torque mentioned above. It is provided by two contrawound spiral springs, one end of each being connected to the top and bottom respectively, of the spindle that carries the coil former. The greater the current passed through the coil, the greater will be the deflecting torque.
The restoring torque provided by the springs will increase in direct proportion to the deflection applied to them. The pointer, carried by the coil spindle will therefore move to a point at which the deflecting and restoring torques balance each other. The springs also serve as the means of passing the current to and from the coil. This avoids the problem of the coil having to drag around a pair of trailing leads.
The word contrawound means ‘wound in opposite directions ’. The reason for winding them in this way is to prevent the pointer position from being affected by temperature changes. If the temperature increases, then both springs tend to expand, by the same amount. Since one spring is acting to push the pointer spindle in one direction, and the other one in the opposite direction, then the effects cancel out.
We now have a system in which the deflection obtained depends upon the value of the coil current. There are still other problems to overcome though. One of these is that the deflecting torque, due to a given value of current, will vary with the coil position. This would have the effect of non-linear deflections for linear increments of current.
If we could ensure that the coil always lies at right angles to the field, regardless of its rotary position, then this problem would be resolved. The way in which this is achieved is by the inclusion of a soft iron cylinder inside the coil former.
This cylinder does not touch the former, but causes a radial flux pattern in the air gap in which the coil rotates. This pattern results from the fact that the lines of flux will take the path(s) of least reluctance, and so cross the gaps between the pole faces and iron cylinder by the shortest possible path, i.e. at 90° to the surfaces. This effect is illustrated in Fig. 3.
Operation of PMMC Instrument
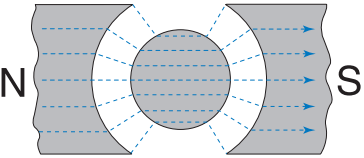
Damping Torque: When current is passed through the coil, the deflecting torque accelerates the pointer away from the zero position. Now, although the coil and pointer assembly is very light, it will still have sufficient inertia to ‘overshoot ’ its final position on the graduated scale. It is also likely to under- and overshoot several times before settling.
To prevent this from happening, the movement needs to be slowed down, or damped. This effect is achieved automatically by the generation of eddy currents in the aluminium coil former as it rotates in the magnetic field.
However, being induced currents means they are subject to Lenz ’s law. They will therefore flow in the coil former in such a direction as to oppose the change that produced them; that is the rapid deflection of the coil.
If the dimensions of the former are correctly chosen, then the result will be either one very small overshoot, or the overshoots are just prevented from occurring. In the latter case the instrument is said to be critically damped, or ‘dead beat ’.
Advantages of the Moving Coil Instrument
The main advantages of the moving coil instrument are:
1. Good sensitivity: this is due to the low inertia of the coil and pointer assembly. Typically, a current of 50 µA through the coil is sufficient to move the pointer to the extreme end of the scale (full-scale deflection or fsd).
2. Linear scale: The deflecting torque is directly proportional to the coil current. Therefore, these meters have linear scale.
The main disadvantage is the fact that the basic meter movement so far described can be used only for d.c. measurements. If a.c. was applied to the coil, the pointer would try to deflect in opposite directions alternately.

Thus, if only a moderate frequency such as 50 Hz is applied, the pointer cannot respond quickly enough. In this case only a very small vibration of the pointer, about the zero position, might be observed. The complete arrangement for a moving coil meter is illustrated in Fig. 4 .
Shunts and Multipliers
The basic instrument so far described is capable of measuring only small d.c. currents (up to 50 µA typically). This obviously severely limits its usefulness. The figure of 50 µA quoted is the value of coil full-scale deflection current (Ifsd) for an AVO meter.
As you will now be aware, this meter is in fact capable of measuring up to 10 A, by using the current range switch. This is achieved by means of what are known as shunts. Similarly, this type of meter is also capable of measuring a range of voltages. This is achieved by means of multipliers.
Both shunts and multipliers are incorporated into the instrument when it is assembled.
Shunts
A shunt is a device connected in parallel with the meter’s moving coil, in order to extend the current reading range of the instrument. It consists of a very low resistance element, often made from a small strip of copper or aluminium. Being connected in parallel with the coil, it forms an alternative path for current flow. It can therefore divert excessive current from the coil itself.
In this instance, ‘excessive current’ means current in excess of that required to produce full-scale deflection of the pointer. The latter is known as the full-scale deflection current, which is normally abbreviated to Ifsd .
Multipliers
The p.d. across the coil (Vc) when Ifsd flows through it is only few mV. Therefore, only few mV can be applied to the coil. It also represents the maximum voltage measurement that can be made. In order to extend the voltage reading range, a multiplier must be employed. This is a high value resistance, connected in series with the meter coil. Thus, when a voltage in excess of Vc is applied to the meter terminals, the multiplier will limit the current to Ifsd